我们帮助您满足需求,实现更具可持续性的发展,并使流程更轻松、更简洁、更安全。 分析将帮助您找到新的可能性。 我们的仪器、自动化解决方案、服务和专业知识将帮助您在金属行业建立您想要的流程控制和质量控制,无论是原料金属还是特殊产品。
在铁、钢、铝、铜和钛工业的高通量、时间敏感性环境下,流程控制和质量控制是至关重要的。 因此,金属生产商必须能够快速准确地分析 其化学品、 金属和合金的结构、粒度和形状以及密度。
金属材料分析种类
-
- 铝
-
从铝土矿到氧化铝再到铝,对材料流实施快速且精准地监测是铝分析流程的关键。通过监测流程相关参数,制造商可以实现其业务目标,并保持流程中各个环节的效率,同时掌控向无二氧化碳金属生产的过渡。借助 Malvern Panalytical 的工业解决方案,您可以分析材料的矿物学成分(Aeris 金属版)、元素成分(Axios FAST、Zetium 金属版)及粒度与粒形 (Mastersizer 3000),并可直接预测流程参数,例如铝土矿中的可用氧化铝、氧化铝的结构变化、铝冶炼过程中的熔池成分,以及铝金属或合金的杂质、应力和结构。我们的解决方案涵盖从实时分析仪器(例如 CNA 交叉带分析仪、Epsilon Xflow 和 Insitec)到全自动实验室等领域的各种产品和服务。
- 炼铁生产
-
在整个钢铁生产过程中,必须对材料流进行快速、准确的监测。制造商必须对流程相关参数进行跟踪,这样才能实现其业务目标,并保持流程中各个环节的效率,同时掌控向无二氧化碳金属生产的过渡。借助 Malvern Panalytical 的工业解决方案,您能够高效分析原材料及铁烧结矿、铁矿石颗粒和直接还原铁 (DRI) 等中间产品,以及钢或钢合金等最终产品。我们的解决方案能够监测各种材料的矿物学成分(Aeris 金属版)、元素成分(Axios FAST、Zetium 金属版)及粒度与粒形 (Mastersizer 3000)。这些解决方案还可以直接预测流程参数,例如 FeO 含量、烧结矿和矿石颗粒的物理参数、金属化程度,以及钢和钢合金的杂质、应力和结构。我们的解决方案涵盖从实时分析仪器(例如 CNA 交叉带分析仪 和 Insitec)到全自动实验室等领域的各种产品和服务。
- 有色金属生产
-
由于有色金属制造商需要实现其业务目标,并向无二氧化碳金属生产过渡,因此快速且精准的监测在其生产流程中至关重要。从矿石到铜、镍和锌钢合金,对材料流涉及的各个环节进行频繁监测对于确保高效流程至关重要。借助 Malvern Panalytical 的工业解决方案,您能够高效分析原材料、中间产品(如沥出物或金属溶液),以及金属成品或金属合金成品。我们的解决方案能够监测各种材料的矿物学成分(Aeris 金属版)、元素成分(Axios FAST、Zetium 金属版)及粒度与粒形 (Mastersizer 3000)。此外,这些解决方案还可以直接预测流程相关参数,例如溶剂萃取和电解沉积的效率、炉渣成分,以及金属和金属合金的应力与结构。我们的解决方案涵盖从实时分析仪器(例如 CNA 交叉带分析仪、Epsilon Xflow 和 Insitec)到全自动实验室等领域的各种产品和服务。
- 金属涂层
-
金属涂层 制造商依靠在生产过程中进行频繁监测来达成其质量目标和业务目标,同时大幅提高流程效率。由于该行业致力于实现无二氧化碳金属生产目标,因此这种分析会变得越来越重要。在镀锌或镀锌退火等各种涂层工艺中,制造商必须快速且精准地进行监测才能确保质量和流程效率。Malvern Panalytical 的工业解决方案可通过高效分析实现流程优化,确保满足各种质量规格。借助涵盖从实时分析到全自动实验室等领域的解决方案,我们的仪器可监测金属涂层的矿物学和元素成分。
- 金属粉末
-
要始终如一地生产具有正确特性的金属组件或产品,制造商需要特性已知且质量可靠的投入材料。对于金属粉末,可能涉及必须使用适当的分析技术进行测量的化学、形态和微结构特性。粒度与粒形是大多数金属粉末工艺的关键特性,因为它们会影响粉末流、粉末包装、孔隙、反应活性,甚至健康和安全。化学的重要性也毋庸置疑,特别是对于粉末冶金和增材制造,其中粉末需要符合指定材料的合金成分要求。晶体结构会影响金属粉末及所制成组件的机械和化学特性。
-
我们的主要颗粒表征解决方案包括 Mastersizer 和 Morphologi 4,两者均为高度自动化的台式仪器。我们的 Zetasizer 系列更适合用于测量金属纳米颗粒和分散体。
-
我们的落地式 (Zetium) 和紧凑型 (Epsilon) X 射线荧光光谱仪均可根据应用要求进行元素分析。对于结构和晶体学研究,X 射线衍射 (XRD) 是我们的主要解决方案,也可提供落地式 (Empyrean) 和紧凑型 (Aeris) 系统型号。
金属可持续性
我们的气候危机正变得越来越紧迫,而金属将在解决这一危机中发挥关键作用。 鉴于这些挑战和机遇,金属生产商正在努力实现无二氧化碳钢等环境目标。 我们创新的金属表征解决方案支持这些努力,使您能够仔细监控您的材料和工艺、提高效率,最大限度地减少材料浪费和能源使用,并防止有毒污染。
金属分析中的 X 射线衍射 (XRD)
金属制造需要依赖出色的分析解决方案,而且了解材料的矿物学和结构特性对于获得高质量结果至关重要。在钢铁生产等高通量工业流程中,效率是关键,但结构分析历来依赖的是湿式化学方法和物理方法。这些方法十分耗费时间和人力,并且不太适合繁忙的工业生产环境。
X 射线衍射 (XRD)
分析方法能够有效解决这一问题,与传统技术相比,该方法能够以更高的规模直接预测流程参数,并且有可能通过自动化进一步提高效率。通过结合元素分析方法,XRD 可针对材料流提供更多的可行见解,从而实现更可靠的流程控制,并使可持续生产触手可及。
XRD 可帮助金属制造行业实现更高的环保目标,例如,该方法可用于分析直接还原铁 (DRI) 的特性,而这在未来的钢铁生产中发挥关键作用。此外,针对在铝生产过程中对电解槽进行有效监测,该方法也提供了高效的解决方案。实验室 X 射线衍射仪(例如 Empyrean 系列)通常用于在钢铁生产过程中对材料的残留奥氏体、应力和结构进行分析。
金属中的痕量元素分析
痕量元素能够通过难以预测的方式改变金属的最终特性。如果未对痕量元素进行监测和控制,它们可能会导致成品出现缺陷,而如果金属部件出现故障或性能不可靠,则可能会产生严重后果。因此,金属制造商需要密切监测其金属材料中的痕量元素含量。由于客户对性能的要求不断提高,因此钢铁制造商必须改进自身的熔炼操作,以将多种化学元素控制在 50 ppm 或更低水平。以这种精度监测元素成分的最佳方法是 X 射线荧光 (XRF) 分析法。
通过有效控制材料中的痕量元素,制造商可大幅改善成品的性能,例如不同温度下的力学特性、低温下的韧性和脆性、可焊接性、冷热成形性和耐腐蚀性。所有这些都是重要的性能参数,因此显而易见,XRF 能够为几乎所有金属生产流程带来切实的价值。
在过去数十年中,Malvern Panalytical 一直致力于为金属制造行业提供 XRF 分析仪器,并积累了丰富的经验,对此我们深感自豪,并且十分荣幸能够帮助众多客户对生产转型进行管理,改为采用更可持续和自动化的未来生产方式。
我们仪器中采用的创新传感器设计和我们为客户量身定制的解决方案能够为不断发展的行业提供切实价值,而且我们项目经验丰富的专家团队可随时为客户提供支持和帮助。
自动化金属加工解决方案
金属生产自动化的势头日益强劲,使研究人员、制造商和金属矿石工人能够更加独立、高效和安全地工作。 这是因为自动化流程支持更频繁的监控,包括在远程环境中。 在马尔文帕纳科,我们通过自动化实验室测试解决方案让金属制造商转向自动化操作。
- 自动化解决方案
- 自动化过程控制解决方案
自动实验室
观看我们的视频,了解自动化实验室的优势:
使用严格的参数更快地监控:在线解决方案
随着监管、竞争和成本压力的增加,金属行业生产商比以往任何时候都更需要提高效率。 通过快速、准确地控制关键参数,实时监控原材料和工艺流程有助于节省时间,减少浪费并确保符合最严格的产品规格。
我们的在线解决方案,包括液体分析仪和鼓风炉输入交叉带分析仪,有助于实现这种实时监控。
Megasa SN Seixal improves autonomy and speed in its analytical chain
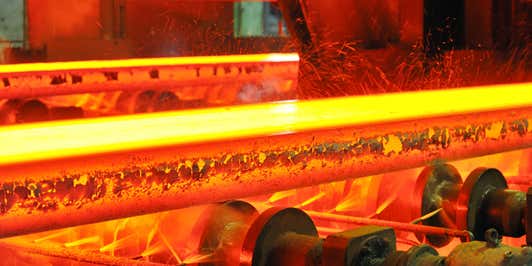