为了以最低的成本生产质量上乘的铝,您需要高效的工艺(尽可能降低能源消耗)以及一致的物料流。经过优化的工艺和材料也可以帮助您实现环境目标。为了预测和优化材料行为,您需要在所有流程阶段持续监控材料,并快速响应结果。
借助 Malvern Panalytical 的工业解决方案,您可以在几分钟内分析铝土矿、氧化铝和铝的矿物、元素和粒度成分,以实现真正面向未来的操作。
您的优势:
- 高效的工艺流程
- 改善的环境影响
- 定制的解决方案
铝土矿开采
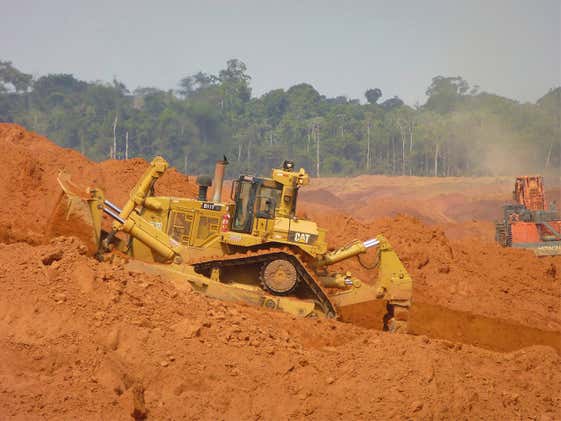
铝土矿 是世界上主要的铝来源,铝土矿石在露天矿中开采,然后再按品级分类。然后对矿石进行化学消解,将宝贵的氧化铝从被称为“红泥”的废料中分离出来。纯化后,将铝金属从电解槽的氧化铝中提取出来。这一过程在世界各地都颇为相似,许多国家都在进行大规模的铝土矿生产。一些大规模生产国包括巴西、澳大利亚、几内亚、牙买加、中国和俄罗斯。
并非所有矿石都是一样的 – 铝土矿存在于三水铝石、一水软铝石和硬水铝石的三个主要阶段。在拜耳消解工艺中,有些需要比其他更高的温度,大多数制造商会优先考虑三水铝石,因为它需要的温度最低,因此消耗的能源最少。要对这些不同矿石进行分类和分级,分析准确是关键。
任何复杂和多步骤过程都需要仔细控制,铝土矿的处理也不例外。在矿场中,CNA 交叉带分析仪可提高矿石分级效率,从而使堆料更井然有序,减少下游资源浪费。
晶相在矿石处理中起着关键作用,通常在像 Aeris 这样的仪器上通过 X 射线衍射进行测量。X 射线荧光用于对元素成分进行特征分析,我们广受欢迎的 Zetium 系列中的 Zetium 金属版,是供工业使用的专业版本。此外,了解颗粒粒度对于氧化铝阶段也至关重要,而 Mastersizer 则是激光衍射的标准解决方案。
氧化铝
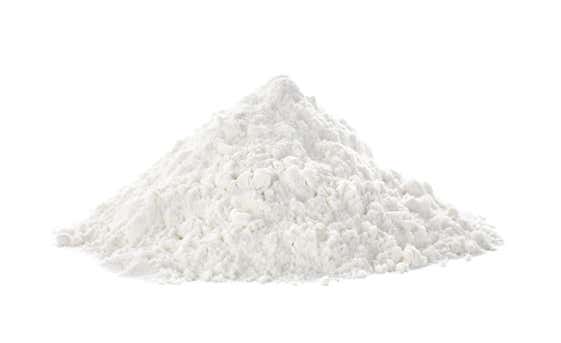
氧化铝 (Al2O3) 是用铝土矿生产铝的过程中产生的中间原材料。颗粒粒度、Al2O3 多晶型或杂质等工艺参数对精炼和冶炼过程中能源和化学品的使用有直接影响,因此影响工艺的效率和盈利能力。
颗粒粒度直接影响冶炼厂电解槽中氧化铝溶解率。此外,细颗粒对健康和安全以及产品运输都是一个问题。氧化铝生产过程中的在线粒度分析将产量提高了 50%,并通过避免重新处理“不合规格”材料,在 12 个月内获得了回报。
了解不同的 Al2O3 改动对于预测和优化冶炼过程中的行为至关重要。γ-Al2O3 是电解所需的多晶型,因为它在冶炼过程中比 α-Al2O3 更容易溶解。因此,必须使用 X 射线衍射 (XRD) 监测氧化铝不同多晶型的比值。
欲推动可持续的金属制造并不断提高 ESG 要求,必须快速准确地监测溶液和红泥中的杂质。我们的 X 射线荧光解决方案可以在过程中和实验室中实时进行元素分析。XRD 仪器可以监测红泥的物相组成,从而确保符合安全和环境标准。
铝测量解决方案
铝冶炼
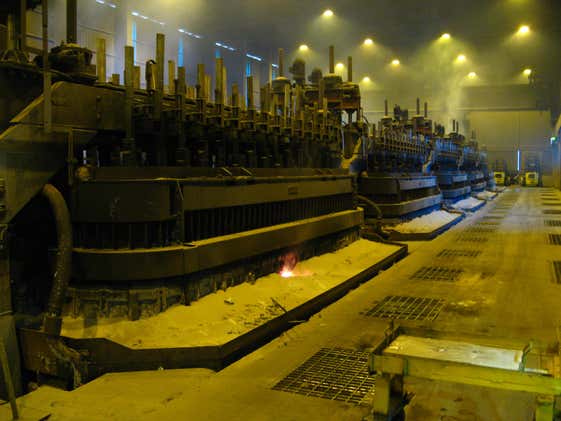
通过电解(霍尔赫劳尔特电解炼铝法)从纯化氧化铝中生产铝需要大量电能。持续监测电解槽组成对于确定、调整和保持最佳状况至关重要,成功执行后可显著节省成本和能源。
X 射线衍射 (XRD)
可助力监测电解槽组成,并快速准确地预测不同类型电解槽(添加钙、镁、锂和钾)的相关工艺参数。该方法可计算液比以及过量 AlF
3
和 CaF
2
,以及游离氧化铝含量和液线温度。
铝冶炼过程中所需和消耗的碳阳极的各自寿命主要由石墨板平均晶粒尺寸 (Lc) 以及颗粒粒度和污染控制。XRD 是一种用于测定晶粒尺寸的标准方法 (ASTM D5178),并在 Malvern Panalytical 的电解槽分析解决方案中实施。
为确保频繁且安全的分析,Malvern Panalytical 提供全自动实验室解决方案,包括根据每个铝冶炼厂的特定需求定制样品制备。
铝加工解决方案
铝合金
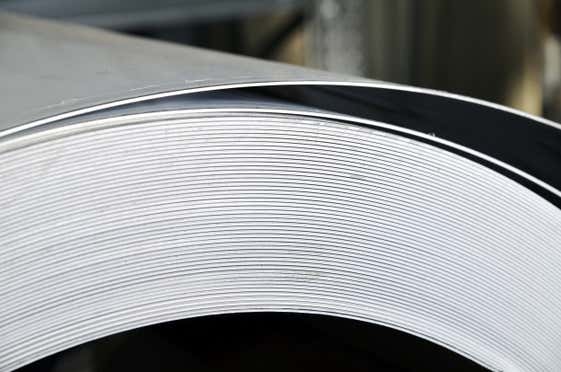
铝金属及其合金在我们的日常生活中随处可见,常被应用于汽车、金属罐、智能手机和飞机中。为保证合金铝或涂层铝的高质量标准,无论铝是由初级原材料,还是由回收材料制成,制造商都必须始终对成分和杂质进行把控。
凭借我们基于 XRF 技术的高通量分析解决方案,您可以对铝金属和合金进行监测,且可以实现自动化并适应每个制造流程。XRD 还可以检查金属属性(如应力和织构),以避免生产出不合规格的金属。
回收铝
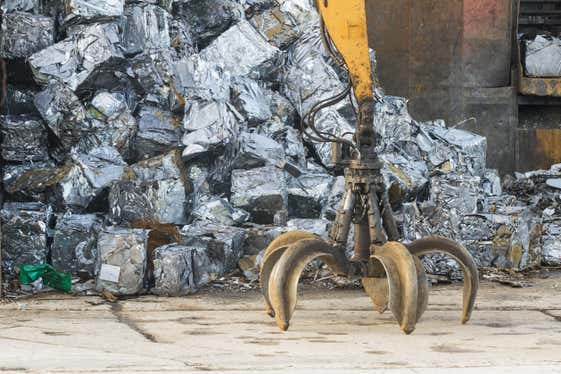
随着金属工业转向更可持续的流程,回收材料正成为降低环境影响日益重要的策略。除了防止浪费,回收材料通常需要较少的加工,因此能源消耗更少。
作为碳足迹较低的商品,回收铝已经越来越受欢迎。但是,使用回收材料后,质量控制和准确分析将变得尤为重要。由于无法控制生产过程,制造商需要深入了解材料属性,以确保安全性和可靠性。
当精度是关键时,就需要专业的解决方案。Malvern Panalytical 的 Zetium 系列 X 射线荧光分析仪包括金属版,专为满足金属工业的特定需求而设计。Zetium 非常适合于严苛的质量控制应用,可助力制造商充分利用回收材料,从而降低对环境的影响并提高盈利能力。
铝分析仪器
相关资源
Optimising aluminium production with on-line particle size analysis
Characterization of metals using X-ray diffraction (XRD) - Residual stress and texture analysis
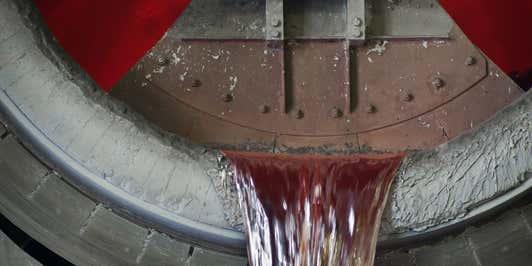